Comprehending Porosity in Welding: Checking Out Reasons, Impacts, and Prevention Strategies
As specialists in the welding market are well aware, comprehending the causes, impacts, and avoidance strategies related to porosity is essential for accomplishing durable and dependable welds. By diving into the root triggers of porosity, analyzing its damaging effects on weld top quality, and checking out reliable prevention strategies, welders can improve their knowledge and abilities to generate premium welds regularly.
Typical Reasons For Porosity
Contamination, in the kind of dirt, grease, or corrosion on the welding surface, develops gas pockets when warmed, leading to porosity in the weld. Inappropriate securing takes place when the shielding gas, frequently utilized in procedures like MIG and TIG welding, is unable to totally safeguard the liquified weld swimming pool from reacting with the surrounding air, resulting in gas entrapment and subsequent porosity. In addition, poor gas protection, typically due to incorrect circulation prices or nozzle positioning, can leave parts of the weld unprotected, permitting porosity to create.
Impacts on Weld Top Quality
The presence of porosity in a weld can significantly compromise the overall quality and stability of the welded joint. Porosity within a weld creates gaps or tooth cavities that weaken the framework, making it a lot more vulnerable to cracking, corrosion, and mechanical failure. These spaces act as stress and anxiety concentrators, minimizing the load-bearing capacity of the weld and raising the chance of early failure under applied tension. Furthermore, porosity can likewise work as prospective sites for hydrogen entrapment, additional exacerbating the destruction of the weld's mechanical homes.
Furthermore, porosity can impede the effectiveness of non-destructive testing (NDT) methods, making it testing to spot various other issues or gaps within the weld. This can bring about significant security worries, especially in crucial applications where the architectural honesty of the bonded components is critical.
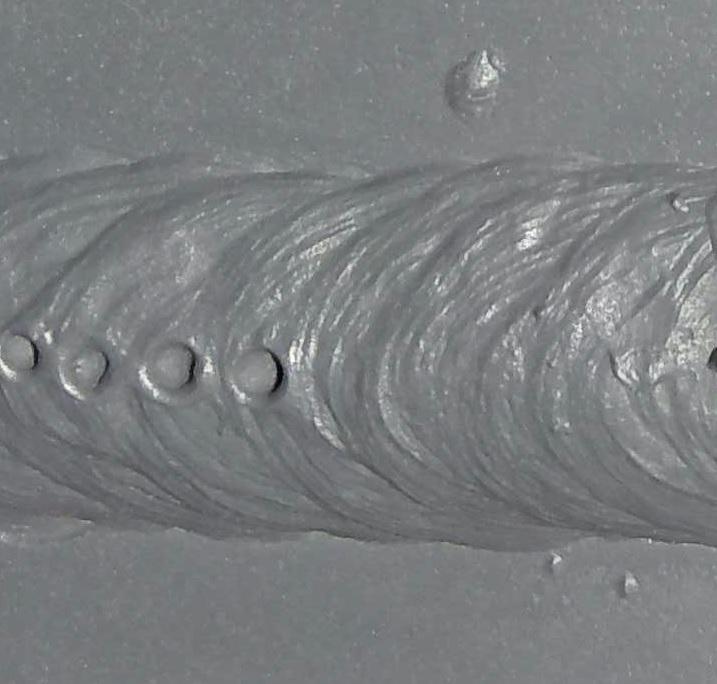
Prevention Techniques Overview
Provided the destructive impact of porosity on weld high quality, effective prevention techniques are essential to preserving the architectural honesty of bonded joints. One of the primary avoidance strategies is thorough cleansing of the base products before welding. Contaminants such as oil, oil, corrosion, and wetness can contribute to porosity, so guaranteeing a clean job surface is crucial. Correct storage space of welding consumables in completely dry problems is likewise vital to avoid dampness absorption, which can lead to gas entrapment during welding. Additionally, picking the suitable welding specifications, such as voltage, current, and take a trip speed, can help decrease the danger of porosity formation. Making certain appropriate shielding gas circulation and protection is another important avoidance method, as not enough gas protection can cause climatic contamination and porosity. Correct welder training and accreditation are crucial for executing preventative steps properly and regularly. By including these prevention methods right into welding methods, the event of porosity can be considerably minimized, leading to stronger and extra dependable bonded joints.
Relevance of Appropriate Protecting
Appropriate securing in welding plays a critical role in avoiding climatic contamination and ensuring the stability of bonded joints. Securing gases, such as argon, helium, or a blend of both, are commonly made use of to shield the weld swimming pool from responding with components airborne like oxygen and nitrogen. When these reactive elements come into contact with the warm weld swimming pool, they can trigger porosity, causing weak welds with reduced mechanical buildings.
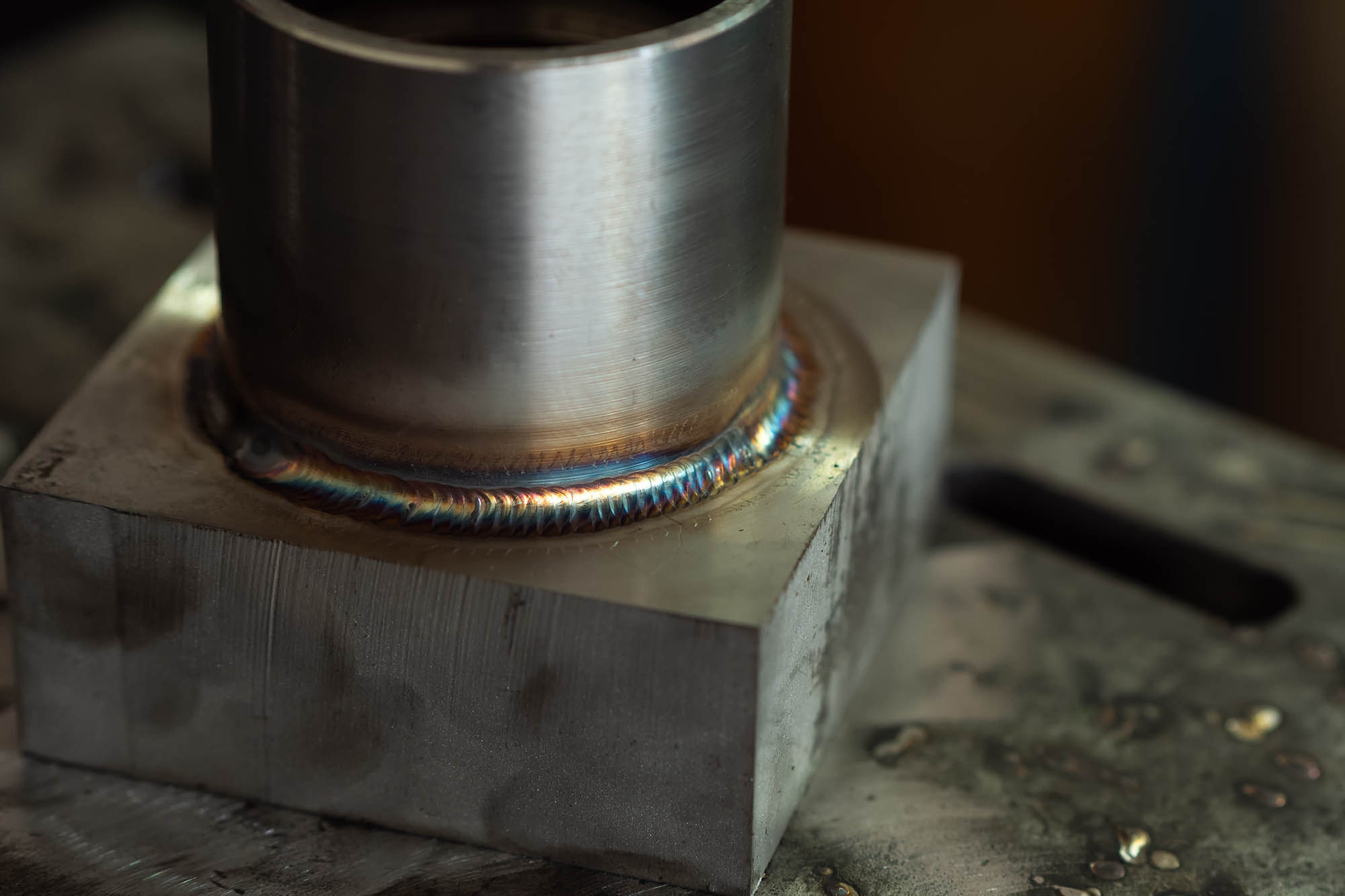
Insufficient protecting can result in various problems like porosity, spatter, and oxidation, compromising the architectural integrity of the welded joint. Sticking to proper securing methods is vital to produce top notch welds with marginal defects and make sure the durability and dependability of the welded parts.
Tracking and Control Methods
Just how can welders properly keep track of and manage the welding procedure to ensure optimal outcomes and prevent problems like porosity? By continuously monitoring these variables, welders can determine deviations from the excellent conditions and make instant modifications to prevent porosity development.

In addition, applying proper training why not check here programs for welders is vital for checking and regulating the welding procedure efficiently. What is Porosity. Educating welders on the relevance of keeping constant criteria, such as appropriate gas protecting and take a trip rate, can assist protect against porosity concerns. Normal assessments and accreditations can likewise make sure that welders excel in tracking and controlling welding processes
Additionally, using automated welding systems can improve surveillance and control abilities. These systems can exactly manage welding parameters, lowering the chance of human mistake and ensuring consistent weld quality. By combining innovative monitoring technologies, training programs, and automated systems, welders can effectively monitor and control the welding procedure to decrease porosity navigate here issues and accomplish top notch welds.
Verdict

Comments on “Professional Guidance on What is Porosity in Welding and How to Address It”